These stories were provided by five of CIM's Industry Partners and originally appeared in the December 2023 - January 2024 issue of CIM Magazine (view it in flip format here).
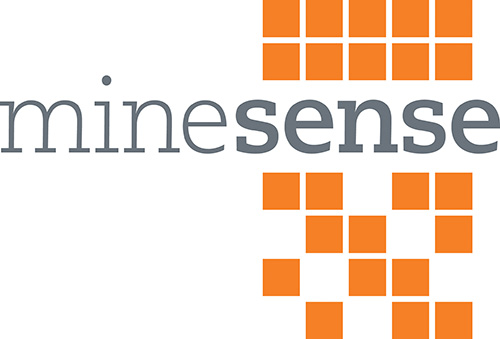
Optimizing the mine-to-mill pipeline with data
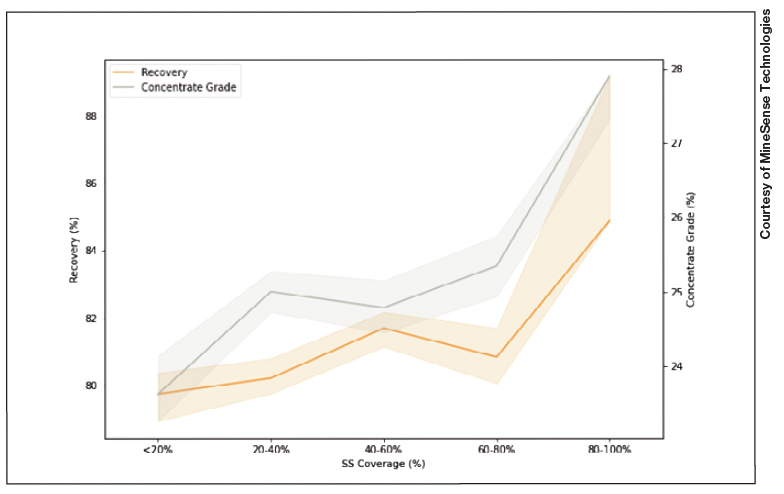
Figure 1. Correlation between ShovelSense® coverage and overall recovery and copper concentrate grade per shift. ShovelSense coverage is calculated as the percentage of trucks in a shift that contain material measured by ShovelSense.
The mining industry faces increasing pressure to improve the sustainability of operations by reducing greenhouse gas emissions, water and power consumption, and chemicals usage. MineSense Technologies helps improve mining sustainability by equipping shovels and belts with X-ray fluorescence (XRF) sensors to enable bulk ore sorting at the mine face as well as downstream process optimization. To accomplish this, machine learning algorithms are applied to the XRF data to characterize the material for every bucket during extraction and along the belt in the grinding circuit.
Automated integration with the fleet management system allows bucket material characteristics to be aggregated to individual trucks so that they can be classified and routed to the correct destination, whether it be recovering ore that would have gone to waste or reducing the amount of waste material sent to the mill. A direct fleet management system integration also enables the tracking of material characteristics measured at the mine face through the full processing circuit and can be linked with downstream sensors such as MineSense BeltSense® systems, on-stream analyzer data or mill assays to provide further processing optimization insights.
The high-resolution datasets generated by MineSense’s ShovelSense® and BeltSense technology allow for smart mining decisions to be made to optimize the entire mine-to-mill pipeline, reducing the environmental footprint per unit of metal produced. For example, advanced machine learning models can be used to extract intrinsic rock properties and predict metallurgical responses of downstream material processing, enabling operators to plan accordingly. These methods have also been applied to quantify the acid-generating potential of waste material and the leachability of ores destined for leach pads to reduce environmental impacts.
Read more: Rio Tinto | Hecla | B2Gold | Teck
On average, each ShovelSense system diverts 5.9 per cent of all measured trucks to waste, which were otherwise designated as ore, and 7.2 per cent of all measured trucks to ore, which were otherwise designated as waste. These estimates were calculated across nine open-pit copper mines equipped with ShovelSense over part of 2023. Percentage diversions vary depending on the amount of contrast in the ore body and in which areas of the ore body the system is operating. For example, high-contrast areas result in more diversions, and more ore diversions are expected when digging through waste. Extrapolated to a full year of production at 90 per cent utilization, digging units equipped with ShovelSense recovered 500 to 9,000 tonnes more copper per year. This equates to an additional $3 to 50 million worth of copper concentrate after taking into account copper price and processing costs, and ultimately leads to an increase in metal production and potential mine life extension.
The second benefit of ShovelSense ore sorting is achieved through removing waste from the ore feed. By reducing the copper grade variability and increasing the head grade of the mill feed, ShovelSense created a more consistent and higher-grade feed to deliver higher recovery and increased copper grade of the concentrate. At one site where these improvements were quantified, shifts with increasing ShovelSense coverage correlated to those with the highest average recovery and head grade (see Figure 1). On average, shifts with 80 to 100 per cent ShovelSense coverage were observed to have a four per cent improvement in recovery and eight per cent more copper in the concentrate than shifts with less than 20 per cent ShovelSense coverage. This is a direct result of ShovelSense increasing copper head grade by 0.03 per cent on average as well as reducing the copper grade variability.
Further downstream improvements of ShovelSense and BeltSense are achieved through operationalizing advanced classification models such as those to predict mineral speciation, acid-generating potential, leachability and grindability of the processed material. This data can be used for advanced waste and ore sorting, or in the case of BeltSense, can be directly integrated into Advanced Process Control (APC) systems in the mill to further improve processing and recovery in a “feed forward” manner. Thus, ShovelSense and BeltSense are proven to deliver high-resolution data that is directly fed into the mine-to-mill pipeline to optimize mining and milling, ultimately leading to more sustainable mining practices.